
Rubber Track Maintenance Tips
How to Maintain Rubber Tracks
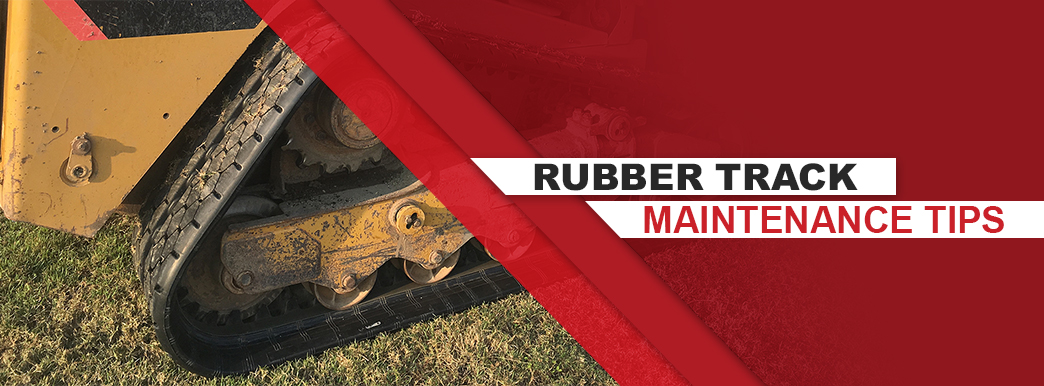
Imagine never providing upkeep to your equipment — your repair costs would soar, and your operations would experience severe downtime. But implementing regular maintenance can increase the performance and life of your machines — and the same goes for your rubber tracks. When you dedicate time to maintaining the tracks, you can create steady operations, a productive fleet and receive the most return on investment.
We devised this in-depth guide on how to keep your rubber tracks in good shape. Using rubber tracks to their full potential is key, so we are here to support you through the maintenance process and to help you understand when your tracks need replacing.
How Long Do Rubber Tracks Last?
The max life for rubber tracks depends on your application, equipment, worker ability, worksite environment, type of rubber and maintenance schedule. There is no specific guarantee on the lifespan of rubber tracks. However, you can optimize track life by being aware of the following factors.
- Application and equipment: Which projects require you to use tracked machines? Depending on the application at hand, your jobs will demand different equipment. From a mini excavator to a skid steer, the lifespan of your rubber tracks relates to the motion of various machines that perform constant or stationary work.
- Worker ability: How an operator drives a tracked machine affects the lifespan of the rubber. Cautiously driving compared to an aggressive style will help avoid long-term damage. You should also train your operators to comply with a strict maintenance schedule.
- Worksite environment: Working on abrasive surfaces such as rock and asphalt will degrade rubber tracks faster than driving on soft surfaces like dirt. Different terrain can cause various stresses on the rubber. Increased wear will limit the track’s ability to perform at optimum levels and decrease its lifespan.
- Rubber type: The quality of the rubber, along with the manufacturing process, will also affect track life. A high-quality compound and technique will increase the usage, durability and flexibility of rubber tracks.
- Maintenance schedule: The life expectancy of a rubber track depends on your dedication to regular upkeep. The more maintenance you perform, the longer the track will last.
Many factors affect the integrity of rubber tracks, ranging from the environment to practicing safe methods. If you want to increase the lifespan of your rubber tracks, maintain strict levels of upkeep on a daily and monthly basis.
Types of Heavy Equipment Rubber Tracks
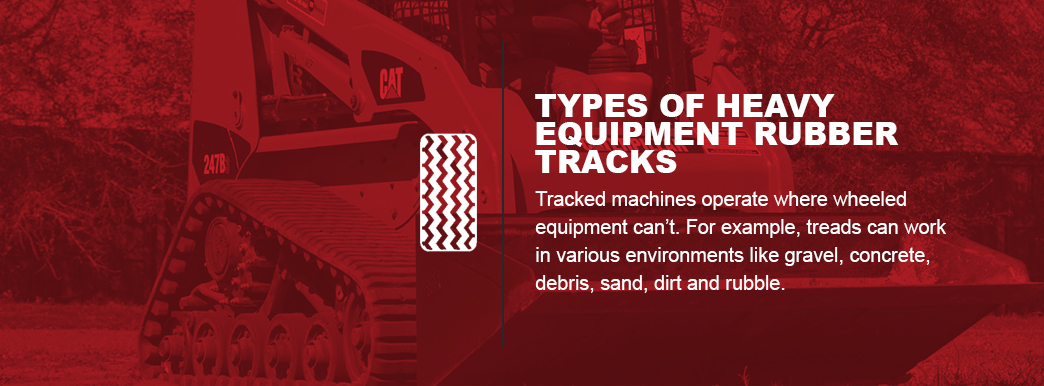
Tracked machines operate where wheeled equipment can’t. For example, treads can work in various environments like gravel, concrete, debris, sand, dirt and rubble. There are four different kinds of rubber treads that can have multiple advantages.
- C-lug: A C-lug track has notches on each block. The durable rubber increases traction and operates better on mud, concrete, asphalt, sand, clay and gravel.
- Multi-bar: A multi-bar solution is ideal for transferring between different types of surfaces, like soft and hard materials. They also do well in snowy terrain.
- Standard block: Standard block tracks are the most popular. They travel well on gravel and hot-paved surfaces. Use them in a range of conditions like lawn, mud, clay, asphalt and sand.
- Straight bar: A straight bar rubber track delivers maximum traction that’s great for wet conditions and mud. They decrease your chances of getting stuck.
Your particular environment and application will dictate which type will best suit your needs. When you need more power to plow through thick mud or snow, choosing the right track will make all the difference.
Competitive Advantages of Rubber Tracks
When comparing rubber tracks vs. steel tracks and tires, you’ll see how rubber tracks can support mini excavators, compact track loaders and multi-terrain loaders in various situations. For example, rubber-tracked equipment can perform well on soft ground and deliver the least amount of damage. The treads glide across surfaces rather like grass and dirt without ripping them up. Where other units may sink, rubber tracks operate well in mud and wet surfaces because of the system’s low ground pressure.
Rubber tracks also more evenly distribute the equipment’s weight compared to tires for increased flotation and better stability. With superior traction over wheels, rubber tracks can travel faster because of reduced vibration from the rubber. The material allows for a quiet operation by absorbing more noise than steel components. By causing fewer vibrations, the rubber enables you to work machines indoors where sound can amplify in a confined space.
Workers who drive rubber-tracked engines will experience more comfort and less fatigue as well because of the rubber’s flexibility. Other benefits include:
- Affordability
- Lighter weight
- Long lifespan
- Lower maintenance costs
- No rusting
The pros of working with rubber tracks give you the freedom to drive on different surfaces without causing damage. The rubber stretches to roll over mixed surfaces, then resumes its original shape. Keeping up with regular maintenance will sustain the advantages of rubber tracks, supporting your bottom line.
How to Keep Rubber Tracks Maintained
Track maintenance requires you and your workers to be proactive. When you’re ahead of the game, you can prevent severe damage that can result in hefty repairs. Keeping up with a maintenance schedule will help your machines run at peak performance levels and reduce the threat of cracking and breaking. Upkeep will also help your ROI stay on track.
Follow our maintenance tips for rubber tracks to preserve the life of your machines and increase uptime.
1. Apply the Correct Tracks
Knowing how to get more life out of rubber tracks starts with installing ones that are the right fit for your equipment. Ensure the rubber tracks have the correct pitch and length to match the sprockets. Investing in the wrong product will cause premature wear on the gears and rubber. The tracks should also parallel the machine’s horsepower.
If you are unsure about your current rubber tracks or which ones you should purchase, rely on expert advice. Professionals will know which tracks best fit your make and model of equipment.
2. Complete Inspections
Proper rubber track maintenance relies on daily and monthly inspections. Before and after each use, operators should conduct a walk-around check, inspecting for missing, leaking or damaged components. Taking several minutes to check the main parts of your equipment and rubber tracks can reduce more severe faults and expenses in the future.
Investigate pieces like the main idlers, drive motor, drive sprockets, rock guards, rollers and track bolts, chains and shoes. Inspect for loose and broken pieces, as well as oil leaks. If you find problems, conduct repairs immediately.
Along with daily walk-around inspections, you should also conduct a more in-depth examination as part of your regular rubber track maintenance every two to four months. Examine the tension of the tracks and check for proper alignment. Look at the machine’s manual for the correct alignment.
3. Drive Up and Down Slopes — Not Sideways
While many projects demand your fleet to travel up and down different grades, do so as little as possible. Not only does it increase operator safety concerns, but operating on a hill can also escalate wear on the track’s guide lugs, rollers and idlers. As you move up or down a hill, keep the drive motor facing the back of the unit for enhanced maneuverability when necessary.
Never travel sideways because it can increase wear and the risk of de-tracking. Turn only on level surfaces and minimize the number of pivots and spin turns. De-tracking can result in severe damage to the equipment’s rubber tracks — and depending on how long an operator continues to use a machine with de-railed tracks, destruction will increase with time.
Skilled workers can often recover a de-tracked unit by employing a few maneuvers, but a track that’s completely off will require full repositioning. Always make sure you’re on stable, level turf and make wide turns when possible.
4. Implement Undercarriage Maintenance
Undercarriage maintenance is one of the most crucial parts of rubber track upkeep. Inspect the sprocket teeth, sprockets, idlers, rollers and other components. Faulty sprockets can pull links out of the tracks, and damaged rollers can affect the rolling area of a rubber track. Replace undercarriage parts as necessary, whether they are worn, broken or cracked.
Cleaning tracks goes hand in hand with undercarriage maintenance. Use a pressure washer to clean off dirt and debris at the end of each use. Take out embedded objects in the rubber and other lodged debris. Removing snow and ice is vital to avoid frozen tracks.
Anything that’s stuck in the lugs, such as asphalt, can grind over time and cause the lugs to drop off the track. Neglecting to maintain your machine’s undercarriage can even cause the recoil mechanisms to flop, resulting in broken track cables.
If you don’t clear out the built-up particles, they can increase the weight of the track and reduce the equipment’s fuel economy. Embedded material can also increase the amount of tension in the tracks, affecting the rubber and other components.
5. Follow Best Practices
Driving equipment with tracks comes with strict dos and don’ts if you want to maintain and increase the rubber’s lifespan. One of the best practices is to avoid continually turning to one side. It can accelerate damage to the sprocket teeth, guide lug, track tread and roller flange. Operators should also concentrate on moving forward in a tracked machine because reverse travel with increased speed places stress on the material.
Your workers should avoid driving on slopes and traveling unnecessarily, as both can increase wear. Keep spinning to a minimum and always operate with both tracks on the same level of surface. Moving with one track on a flat surface and the other turned on a mound, curb or stone can crack the rubber and compromise the track’s effectiveness.
6. Maintain Site Conditions
Although rubber tracks can support a range of work conditions, they perform best on soft surfaces such as dirt, clay, sand and turf. If possible, avoid worksites that have paved and rocky ground that can cause abrasions, chipping and cuts. Look over your site and eradicate any hazards, sharp objects and other elements that can inflict damage on the rubber. When applicable, use your tracked equipment in the most appropriate environments.
7. Make 3-Point Turns
Stray from making sharp, fast, 180-degree turns. Instead, make three-point turns to reduce side wear. Gradual and full movements will help keep the rubber from skidding across rough and uneven surfaces. The technique is especially helpful when driving compact track loaders and helps prevent tip-overs, keeping workers safe.
8. Maneuver Around Curbs
In some worksites, it may be tempting to drive over curbs to reach your destination faster — but don’t do it. Curbs put excessive stress on rubber tracks and can cause de-tracking. De-tracking is unsafe and damages the tracks and undercarriage. If the track doesn’t sway when rolling over a curb, cracking can occur instead.
From there, everything else becomes impacted. Rubber can fall off in chunks, exposing the internal steel cords to moisture. Any contact with moisture can cause corrosion and track failure. It becomes a domino effect on the remaining equipment components.
9. Rotate Tracks Regularly
Maintenance for rubber tracks involves the same concept as rotating the wheels on a car. Rotate your unit’s rubber tracks according to your maintenance schedule to dodge uneven wear. Always replace both tracks at the same time to ensure even treads. Alignment issues can occur if you only replace one, and unaligned tracks can lead to undercarriage damage as well.
10. Sidestep Excessive Tension
It’s a longstanding myth that owners and operators should keep the tension of their rubber tracks extra tight to help them last longer. However, some leeway and flex are necessary. Excessive amounts of pressure can cause idler and bearing wear, power loss and torn tracks. Without proper tautness, the tracks can experience premature wear.
Tracks with not enough tension can also affect the planetary drive wheel cleats, resulting in de-tracking. A rubber track that’s too loose can damage the machine and increase safety concerns.
Adjust the tension as necessary, according to the manufacturer’s recommendations. Each OEM manual will have different requirements for different sized engines. Check the tension each week by measuring the middle of the roller for the right amount of sag.
11. Store Tracks Correctly
As each workday comes to an end, appropriate fleet storage is essential to maintain a machine’s rubber tracks. If outside storage is your only option, cover the entire unit or park it in the shade. You can also individually cover the rubber tracks with tarps or cloths.
Keeping the rubber tracks hidden from UV rays is critical and can double the track’s life because the sun causes the treads to wear faster. Store heavy machinery indoors in a cool and dry location whenever possible.
During off-seasons — or if you don’t use your tracked equipment every day — run the engine at least once every several weeks to help maintain the flexibility of the rubber. If the machine will be in storage for an extended time, take off the tracks and lay them on their side. This puts the material in a relaxed position and prevents misshaped rubber. It also prevents folds and crimps.
12. Travel on Appropriate Surfaces
Tracked multi-terrain loaders, mini excavators and other units can withstand a variety of environments. However, take precautions and avoid the following applications.
- Concrete and asphalt when turning
- Corrosive materials
- Iron rods
- Jagged stone and base rock
- Quarry, demolition or recycling applications
- Rebar
- Roots
- Scrap iron
- Sharp debris
- Soil with large amounts of rocks
Even though tracks can’t puncture like wheels, sharp objects can slice the rubber, and other threats can affect the track’s internal steel cords. Avoiding harmful contaminants such as salt, oil, manure and chemicals is crucial. These substances can cause the rubber tracks to deteriorate.
Also, be aware of oil and grease that leaks onto the tracks from other internal components. Rinse and clean your tracks every day to ensure the integrity of the rubber and to eliminate harmful chemicals.
Understanding the 12 main tips for maintaining rubber tracks can result in improved performance, safety and efficiency, as opposed to excessive downtime and expensive repairs. Each technique will increase the longevity of your rubber tracks and help support your operations to boost your bottom line.
Rubber Tracks for Different Machines
Rubber tracks can accommodate a variety of equipment types, surfaces and applications. When you upgrade from OEM tracks to highly engineered, new rubber solutions, your engines will experience a multitude of benefits.
1. Compact Track Loaders
The compact construction of these machines makes them portable yet powerful. With enhanced traction and stability compared to wheeled skid loaders, compact track loaders have excellent digging and lifting abilities. However, it can only adapt to different situations if the track is versatile as well.
Standard OEM rubber tracks can support a range of applications, but when you upgrade to heavy-duty tracks, the equipment undergoes a boost in productivity and performance. High-quality rubber has reduced wear and tear, too.
2. Multi-Terrain Loaders
Also known as MTLs, multi-terrain loaders support high performance when working in more delicate environments. Because of their low ground pressure, the machines are ideal for traversing over soft ground, unlike compact track loaders. MTLs offer a smooth and comfortable ride because of the suspended undercarriage.
Installing the right track onto a multi-terrain loader can enhance the durability of the machine. The proper rubber tracks can also deliver a higher level of versatility. Switching to a sturdier track compared to the OEM version can offer advantages such as a longer lifespan, better value, exceptional performance and less downtime.
3. Mini Excavators
Mini excavators are one of the more portable machines on the market, and they come in a range of configurations and sizes to support every industry. They are versatile enough to take on dozens of projects. Modify your OEM or worn excavator tracks to a high-quality rubber for increased performance and stability. Working with better rubber tracks allows you to get more out of your unit due to the improved efficiency.
4. Carrier Dumper
Also known as track carriers, dump trucks with rubber tracks offer superior traction. They deliver more rugged performance when compared to regular dump trucks. Carrier dumpers are compact, allowing them to maneuver in places conventional vehicles can’t.
They are ideal for construction, landscaping and material handling and work well in rough-terrain conditions. Upgrade the rubber tracks for enhanced durability and look for multi-terrain, high-performance solutions to improve the strength of your unit.
5. Aerial Platforms
Stability with aerial platforms is crucial because the equipment lifts people and tools to reach higher access points. Move on from your OEM tracks and benefit from reduced vibrations with more advanced aerial rubber tracks. Better engineered tracks can also protect indoor surfaces with non-marking features.
6. Harvesters
Harvesters with upgraded rubber tracks are tough enough to get through the various types of surfaces in the field. Installing new harvester tracks with more wear resistance and better tensile strength can support the reaping, threshing, winnowing and cleaning processes.
Knowing that you can replace your old, worn or OEM rubber tracks with advanced solutions can help your machines to operate on multiple surfaces and applications.
When to Replace Your Tracks
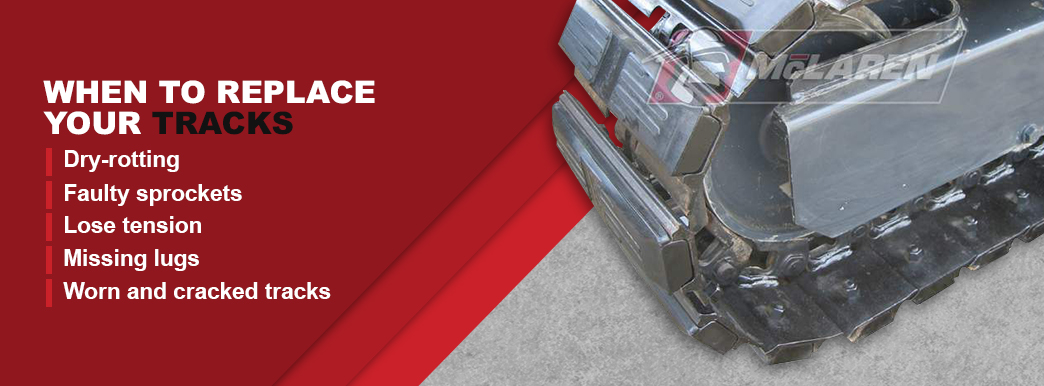
While maintenance can prevent cracks in the rubber and more severe damage to a track’s steel cords, you will eventually have to replace your rubber treads — but you shouldn’t wait for complete failure. Look out for the top five signs that indicate your equipment’s tracks need replacing.
- Dry-rotting: Stress marks on rubber can cause the material to rot from exposure to the elements and various jobsite environments. Rotting can affect the strength of the rubber. Replace the tracks if rotting occurs.
- Faulty sprockets: Sprockets and tracks work together to enable smooth operation. When the gears begin skipping over the lugs, a loose track or worn sprocket can form an uneven mesh. It can also cause the tracks to de-rail. Through your regular maintenance schedule, make sure the sprockets are in excellent condition and replace the rubber tracks and gears if they begin skipping.
- Lose tension: Check the tension of the track each day and make corrections as per your manufacturer’s suggestions. Tracks can loosen over time and can become permanently slack, which will require replacement.
- Missing lugs: When debris gets packed into the crevices of a track, the lugs can fall off. This problem can also occur because of worn sprockets. Replace the lugs when necessary and install new rubber tracks.
- Worn and cracked tracks: The exterior of the rubber will crack over time. Although maintenance prolongs the track’s life and prevents cracking and wear, working on rough terrain can increase the chances of damage. Rolling over curbs, aggressive driving and not adhering to best practices can also lead to rubber flaws. Replace the treads when cracks appear.
Not keeping up with the tension of your tracks is a good indication they need to be replaced. Tracks that are too loose or too tight can cause damage to the rubber and cause it to lose its proper shape. If your tracks are dirty and debris is stuck between the grooves, the rubber may wear faster. Maintaining the cleanliness of your equipment is vital.
Another way to tell if tracks call for replacing is if you disregard undercarriage upkeep. If you fail to perform inspections, the rubber can wear from the inside out. A faulty undercarriage can also cause more damage to components such as sprockets and idlers.
If you’re experiencing any of these problems or know you neglect certain maintenance tasks, you need to replace your rubber tracks.
Finding the Right Track Size Is Key for Better Performance
After recognizing the signs that you need to replace your tracks — or if your rubber tracks experience complete failure — choosing the correct track is your next step. If you install an improperly sized track, it can lead to faster wear, reduced productivity and increased safety concerns. Because the usage of rubber track solutions must parallel the product’s size, you want to consider three things — tread pattern/links, pitch and width.
When you’re looking to replace damaged and worn tracks with new rubber treads, the first step is to determine the size of your current OEM track by checking the stamp on the rim. If the mark is worn, you can measure the track for an accurate scale.
1. Tread Pattern/Links
Count the number of lugs or links around the track to determine if you have turf-friendly or aggressive links. The former has more contact points with the ground to create less pressure. The lugs are also closer together, creating less of an impact on worksite surfaces. An aggressive type may have a zig-zag pattern and prominent lugs for better traction in wet conditions.
2. Pitch
Determine the pitch of the track by measuring the distance between the center of one link to the center of the next. Short pitches engage with each sprocket tooth for a smooth ride while long pitches contact every other sprocket.
3. Measure the Width of the Track
The width of the track should match the machine. Wider solutions have enhanced flotation and more surface area for boosted traction. They are also ideal for applications that don’t involve space issues. Narrow surface areas are more economical. Compact machines do well with a profile track, making the units perfect for landscaping and other applications that require a smaller footprint and advanced maneuverability.
Once you check the width, pitch and links, you will want to measure the guiding system. Find the trough located down the inside of the rubber track. Measure the outside guide bottom by measuring the distance between the outside, bottom portion of the lug to the outside bottom of the lug across from it. Then, repeat the step, but measure the inside of the lugs. Next, find the inside height of the lug.
A compilation of the measurements will help you determine which size rubber tracks you need to purchase. Make sure you choose tracks that are designed to fit the make and model of your equipment, whether you have Cat®, Kubota, Volvo, Bobcat, Terex, JCB or John Deere. Also, consider the features you want your new tracks to ahve. You may be in search of more traction or less surface damage. Look for tracks that emhasize the capabilities you need most.
Installation Techniques
Safety is the primary concern when learning to install a new rubber track. Always wear safety equipment like gloves and protective eyewear, and make sure that the engine is off and the machine is on a flat surface. Notify other workers to keep clear of the area until the installation is complete. Work in an area where you won't disrupt the workflow of other heavy equipment.
The fitting process involves more than two people — if not an entire crew for support. For larger tracks, use the help of other heavy machinery, like a forklift.
If the equipment has a durable frame, you can often use the machine’s boom to lift the unit. If not, you can use jacks and support stands. Having the proper tools to remove the following components is also vital.
- Control valve linkage
- Grease valve and cover
- Sprocket segments
- Steps
- Top carrier mounting bolts
Follow the next two sections to learn how to take off faulty tracks and how to replace them with new rubber.
10 Steps to Take Off Old and Worn Tracks
- Loosen the track adjuster valve to release grease and then remove the valve altogether.
- Place a pin in the cleat and rotate the track. Roll the rear idler onto the pin to collapse the track adjuster. Remove the bolt, clean any excess grease, tighten the grease valves and remove the top carriers.
- Dismantle the triangle plates from the rear bottom rollers and take off the linkage from the other track drive pump. Lift one side of the unit off the ground by using the boom and put supports underneath the machine.
- If the sprockets are a single piece, don’t move them. If they remove in segments, take out three and leave one.
- Double-space three pins between the cleats under the rear idler.
- Rotate the equipment to lift the pins from the cleats, clearing them from the idler.
- Wrap a strap around the track, near the middle/upper portion of the rear idler, and pull the track off as the pins act as a slide.
- If you have one segment of the sprocket, adjust it to the rear and remove the step.
- Drop the track from the driving house by pulling on each end with the straps and remove it from the rear idler. Work the track out of the front driving house and under the machine with the straps.
- Inspect each undercarriage component.
Installing New Rubber Tracks
- Push the track to the center of the frame and keep it aligned.
- Lift the track onto the pry bars of the frame, working it onto the sprocket and drive end.
- Segment sprockets will require you to rotate one to the left so it points upward to keep the track on.
- Push the track’s lower segment under the bottom rollers. Lower the support to lock the track onto the inside of the rollers.
- Push the track onto the rear idler until you reach the cleats. Then, place two pins in the cleats at the rear idler bottom.
- Rotate the machine around the rear idler to guide the rubber onto the track.
- Apply the triangle plates and bottom rollers. Use a forklift if possible for the rollers.
- Lower the unit and reinstall the upper rollers.
- Adjust the track to the proper tension.
Installing new rubber tracks can be a challenging task, whether you need new tracks for a mini excavator, a standard compact track loader or another type of equipment. If you need additional help during the installation process, reach out to professionals for support. Adding new rubber to your machines will improve safety, productivity, efficiency, fuel economy and the lifespan of your equipment.
Find the Right Rubber Tracks at McLaren Industries
McLaren Industries has 25 years of experience in designing and engineering rubber tracks for a variety of equipment types. Our products range in size, make, model, fit and pattern to accommodate major brands like Cat, Kubota and John Deere. Our in-house engineer team uses a complete vertical integration process to develop a high-quality rubber.
We are here to support your rubber track maintenance needs, as well as other components that come with track solutions. Browse our rubber tracks or contact us online to speak with a real McLaren professional. We can support your operation’s productivity, efficiency, safety and bottom line, no matter the industry.
Request a Quote